Q&A: Markus Thiel gives fascinating insights
Welcome to our employee interview series - starting with Markus Thiel.
In this series, we give you an exclusive behind-the-scenes look at the people who drive our company with passion and dedication.
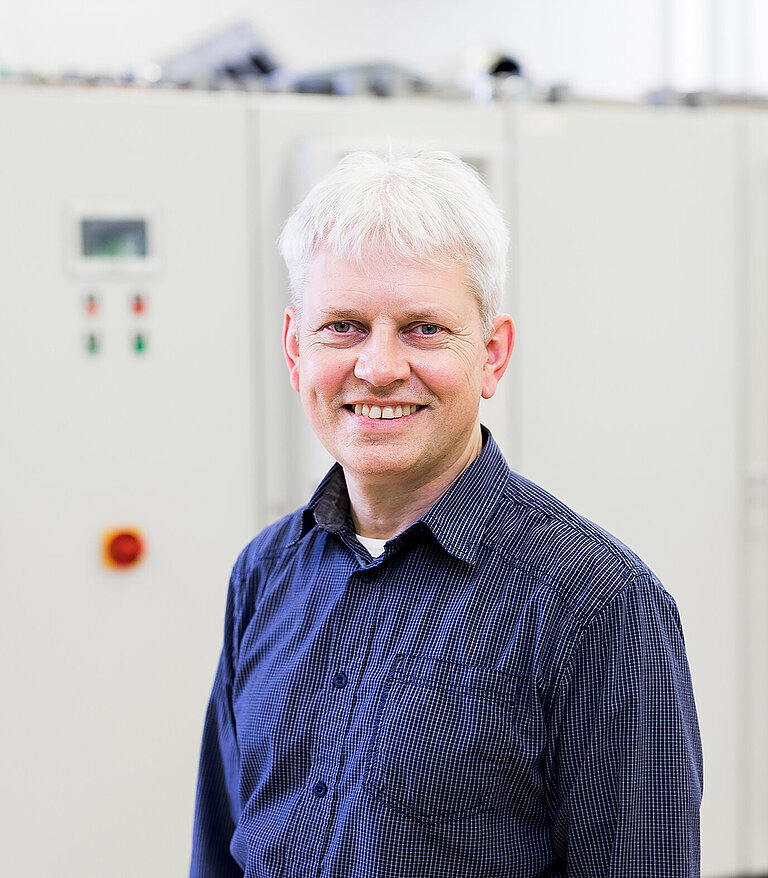
I am working at Plasmatreat since July 1994. I did several, different jobs and now I am group leader of the electrical design team.

Markus, what were your first impressions when you joined the company?
I remember my job interview very well. It was supposed to be with several people, but it quickly turned into an intense conversation with the person in charge. Even during the interview, he showed me practical applications and his enthusiasm for innovation and technology was immediately transmitted to me.
A particularly memorable moment was when I entered a dark room with corona discharges sparking everywhere - a fascinating spectacle that immediately piqued my interest. Another memorable moment was when I was shown a transformer - not in an ordinary case, but in a simple plastic bucket. This unconventional, creative thinking made a lasting impression on me.
After the interview, things were quiet at first. I didn't hear anything for four weeks until I finally called to inquire. The secretary told me they wanted to hire me - they just hadn't gotten around to calling me. An unusual start, but one that was more than worth it!
Markus, how do you think the company has changed over the past 30 years?
The first ten years were a transition from a start-up to an industrial company. In the beginning, a lot of things were still in the tinkering stage - everyone did everything from quotations to assembly and training. Today, the tasks are much more specialized. The development to a global company with 300 employees is impressive. I am particularly proud of our certifications, such as UL or CE, which we worked on for many years. Perseverance has been the key to success.

Markus, what was the most challenging project you have worked on, and what did you learn from it?
The most challenging project was an automated plasma cell for an automotive supplier in Illinois, USA. It was my first trip to North America and I didn't know exactly what to expect. Together with my colleague Guido Marks here in Germany, we assembled and commissioned a complete cell on site within ten days. We divided the work between us: While Guido slept in Germany, I developed ideas in the US and passed them on to Germany. While I slept, Guido drew up e-plans and production documents, which I then implemented the next day in the USA.
This project showed me that with a structured approach, you can achieve more than you think. It was a milestone for me.
Markus, what successes or achievements are you particularly proud of?
I am particularly proud of the light control module I developed for plasma monitoring. It provides continuous process control and is still integrated into every one of our nozzles today. There are also systems I designed more than 25 years ago that are still in use. This long-term stability shows how sustainable our work is and how functional our systems and plasma technology are.
Markus, how would you describe the company's culture?
Our culture has evolved as the company has grown. We have grown from three to 300 employees, and yet we have maintained our flat hierarchies. This is a great advantage. The team spirit is strong. Everyone has a sympathetic ear, no matter what the problem is. This team spirit is one of the reasons for our success.

Markus, were there any mentors or role models in the company who inspired you?
Definitely. Mr. Buske and Mr. Förnsel, who were both involved in the founding of the company, made a lasting impression on me with their innovative spirit and diversity of ideas. Mr. Christian Buske in particular inspired me with his courage to expand the company globally at a very early stage and to always think outside the box. This out-of-the-box thinking has made us the global market leader.
Markus, how have your roles and responsibilities changed over the years?
I have worked in almost every core area of the company. In the beginning, I spent a lot of time in the field, training customers and giving presentations. The assignments in Japan, China and Thailand were particularly exciting. The cultural differences were often a challenge, but they broadened my horizons. Today, as electrical design team leader, I focus on developing my team and promoting younger colleagues, while always keeping an eye on electrical design challenges.
Markus, what are your hopes for the future of the company?
I hope we can maintain our flat hierarchies and continue to drive standardization. This is the only way we can react quickly and remain competitive. We should continue to develop our unique selling point in the PlasmaPlus area and open up new applications.
Markus, what advice would you give to new employees?
Be flexible and open to new things! Decisions sometimes have a short half-life, and you have to be able to deal with them mentally. It's important to enjoy unconventional approaches and adapt to the circumstances.
Markus, what else would you like to learn?
I would like to learn how to respond better to the different generations. Each generation has its own way of thinking, and you have to find the right approach to pass on knowledge successfully.
Markus, is there a particular experience or anecdote that stands out in your mind?
After the first pretreatment trials, we always tested whether the plasma pretreatment was successful by having me go to the tap. That was the most original form of test ink, but it worked and shows how pragmatic we often were.
We would like to thank Markus for this time and these exciting insights in how working at Plasmatreat developed in the last 30 years.